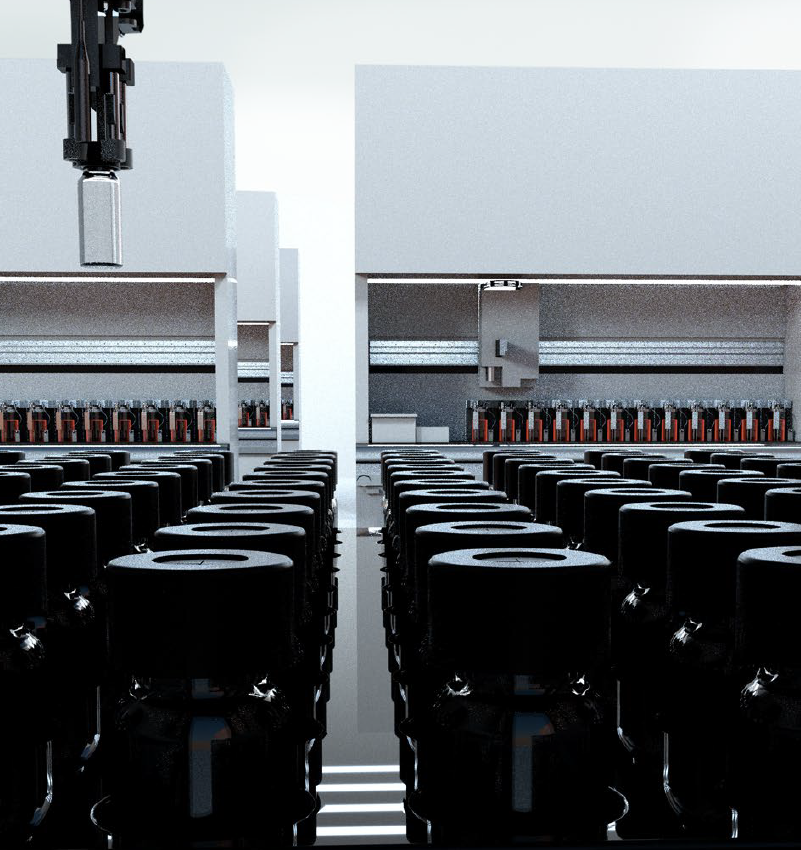
SampleBus
Advanced Autosampling for Ambr® 250 Multi-Parallel Bioreactors
Built on the back of Securecell’s own next-gen high-throughput Integra1 64 development, we have discovered a seamless automated flow to continuously sample each bioreactor of up to six Ambr® 250 systems four times every 24 hours.
This highly customizable solution delivers the ultimate control together with Siemens PLC and Lucullus Bioprocess SCADA. This set-up works day and night with the industry’s top analyzers to achieve the highest level of insight for process development and optimization for your Ambr® 250 systems.
Ambr® is a registered trademark of “The Automation Partnership (Cambridge) Limited”.
Module Basic
Ambr® 250 Sampling Process
Ambr® 250 Sampling Process Flow
- Load 3 empty vials on a conveyor belt
- Sampling process: transfer 1.5ml sample into one vial via Sample Transfer Unit
- Transfer the sample vial and two empty vials Into High Density Filtration / Sample Prep Station
- Return the sample vial with 0.5ml Cell Suspension to a conveyor belt
- Transfer suspension sample to Cell Analytics (vortex, dilution)
- Transfer the cell-free sample (0.8ml) to the conveyor belt
- Deliver 100ul sample to UPLC Amino Acid Analyzer
- Deliver 100ul samples to CQA Product Analyzer
- Deliver 500ul to Substrate Analyzer (glucose, lactate, NH4, ions)
Expanded System Architecture
Example: 4 Ambr® 250 Systems Connected by Bus and Sub-Bus to Analytics
- Vial Transfer Unit transfers vial from Sub-Bus to Main-Bus
- Sample Transfer Unit transfers processed sample into vial
- High-Density Filtration and Sample Prep Station (HDF-SPS) performs filtration
Filtration
HDF-SPS (High Density Filtration and Sample Prep Station)
Key Features:
- Sampling via Ambr® 250 < 2ml into SEC cell (qualified in Numera project)
- Centrifugation for cell and debris removal 2000g - 10,000g
- Optional final filtration via Sephara™ membrane (yield 1.0 ml)
- Any cell concentration (up to 200 million cells per ml) can be filtrated with exceptional yield of supernatant
-
Sample Sub-Bus
-
Rotary gripper
-
2D-Code scanner
-
Centrifuge
-
Vortex mixer
-
Scale
-
Syringe 5 ml
-
Syringe 10 μl
-
Vial magazine at 4°C
-
Vial magazine at 37°C
-
Vial magazine at 80-90°C
-
Vial Magazine at room temp.
-
Counterweights
-
Portal robot
-
Waste bin
PAT Performance Capabilities
-
It’s Time to Update Your Algorithms
-
Up to 6 Bioreactors from 6 Ambr® 250 systems can be sampled in parallel
-
Each bioreactor can be sampled every 6 hours or 4 X per day (8 X per day is possible with additional analytical equipment*)
-
Compatible with most analytical systems on the market (Cedex®, UPLC/LCMS, Nova FLEX, etc.)
-
-
Structure of Vial Holder
Each vial holder has several functional attributes that allow you to insert, transport, unload and remove vials from the structure.
Along conveyor belt, several functional stations can be allocated to serve different functions including loading, unloading, and sample transfer.
SampleBus Concept
Vial Loading Station
- The loading station can host 16 racks with total 2,048 vials
- Elevator mechanism removes exhausted rack from loading position
- Station can run unsupervised, providing uninterupted sample vials for up to 5 days
- High precision and transport security
Usability Concept
Local Interaction
- Simple, intuitive, powerful control
- Siemens Touch-Panel
- No Planning is necessary. Implicit rules manage all
- Lucullus-Interactions limited to administrator access
The SampleBus connection to the Ambr® system utilizes the openly accessible and documented OPC interface In order to synchronize the sampling process.
Ambr® is a registered trademark of “The Automation Partnership (Cambridge) Limited”.