
Despite all the advantages the iCELLis® reactor systems have, they still operate as individual units and overarching process monitoring and control of multiple iCELLis® reactors and other peripheral devices is not standardly available. However, such overarching process monitoring and control capabilities were strongly desired by operators at IDT. A major complication to achieving overarching operation of the various scales (iCELLis® Nano, iCELLis® 500) are the different types of control units that control the vessels. The iCELLis®Nanos are controlled by Applikon my-controls, whereas the iCELLis® 500 are using a very different automation platform by Pall. Thus, standardized and centralized data logging, process control, and reporting were inherently difficult and not to be solved by either of the two hardware vendors. Furthermore, the operators at IDT had the desire to flexibly design their process control recipes (step-chains) themselves without dependency on the hardware manufacturer which was often accompanied by long lead times and unnecessary financial efforts. In conclusion, Securecell AG was onboarded by Applikon BV for this integration project.
Navjyot Waghmare (Automation Expert at IDT) was leading the subsequent project that resulted in Lucullus® empowered iCELLis® reactors in validated environments at IDT in its sites in Dessau-Rosslau and in Magdeburg supporting vaccine production to date. But first things first: The initial installation encompassed the integration of 4 iCELLis® Nanos and an iCELLis® 500 reactor in Lucullus® at IDT Dessau in the year 2017. Specifically engineered product improvements were also part of that implementation and exemplify Securecell’s service promise and competence. One new feature that was implemented upon feedback from IDT was a configurable user interface allowing interactive piping and instrumentation diagrams (P&ID) to operate the equipment (Figure 2). This is a nice example of how proactive customers contribute to the targeted development of Lucullus® based on real use cases (from which other customers still profit today). In the following, Lucullus® was tested thoroughly and as a result, is operating in that validated production environment thus far.

In the subsequent years, Lucullus® was adopted at the IDT development site in Magdeburg on another set of small-scale iCELLis® Nanos. Also, the initial installation in Dessau was recently extended by the integration of four additional iCELLis 500+, the newer generation of large-scale iCELLis® reactors, in September and November 2021, and now spans across four labs in a robust, distributed client-server architecture (Figure 3).
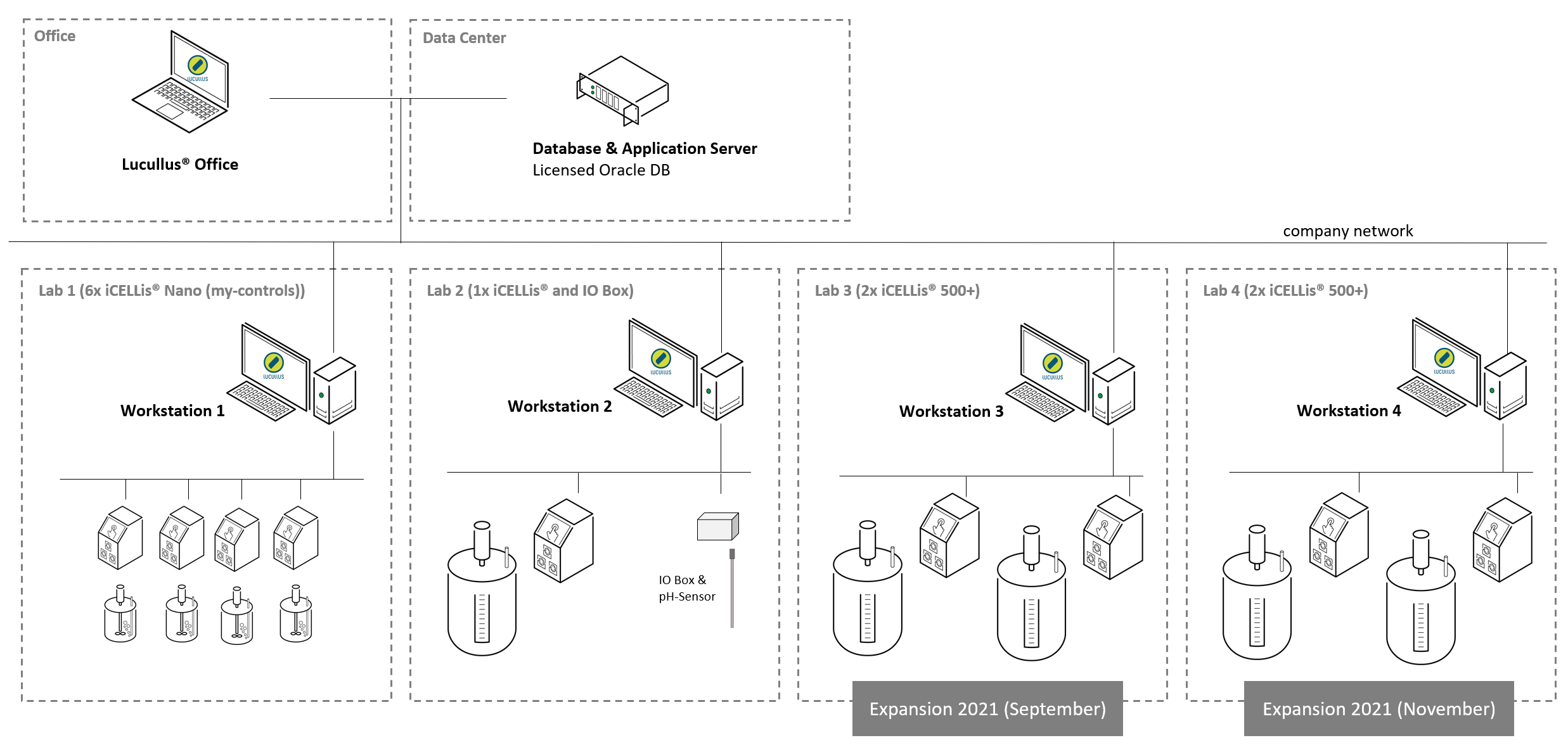
With Lucullus®, IDT process engineers can nowadays flexibly implement automated process control recipes to allow for quicker project adaptions. The operators can rely on unified monitoring and control interfaces built according to their needs. All data, including contextual information about the processes, is securely stored in a centralized database in a harmonized manner. Together, IDT and Securecell realized a performant bioprocess infrastructure with Lucullus® as the digital backbone, ensuring data integrity, greater efficiency, and increased capacity for IDTs offerings as a CDMO. This unique flagship implementation on fixed-bed production vessels will help IDT to manufacture and deliver high-quality and safe vaccines.
Both companies are now looking into handling Lucullus® life-cycle management of the installation in the validated space which means going through an update process. Within the framework of the renewal, IDT will profit from the new, ever-improving, and increasing Lucullus® functionality. Specific examples are the REST API interface to facilitate data export to 3rd party data analysis and modeling tools, manual user interactions along the automated process or improved reporting to name just a few.
Within the last five years, we have successfully integrated bioreactors at IDT in Lucullus® for GMP processes. In the future, the goal of both companies is to upgrade the Lucullus® software to the expert version, which will enable complete process digitalization from the planning until the process execution phase and further automate and digitalize GMP processes at IDT.
"We are using the iCELLis® systems for many different processes and customer applications. Therefore, it was important to have a software solution like Lucullus®, which is flexible and can be easily adapted in a short time for new processes. The implemented P&ID function helps us to adapt the operator screen without dependence on system suppliers and oversee the critical process parameters." |